History of the SeaCAT
SeaCATs, the CTD family consisting of the 16plus V2 and 19plus V2, were first developed in late 1985 back when Sea-Bird had barely evolved past a garage operation. When a customer requested a moored CTD – the first that Sea-Bird had ever built, Sea-Bird’s team developed the first model. At the time, Sea-Bird’s staff mostly consisted of a handful of engineers. Unfortunately pictures of the first SeaCAT have been lost to time (probably because that early design didn’t last long) but some of those initial engineers still remember the design.
Unlike the current versions – the 16plus V2 and 19plus V2 – where the conductivity cell is installed on the side of the housing, the first design had the conductivity cell atop the endcap next to some connectors, like a sausage resting on a plate. The endcaps were secured to the housing with external aluminum rods that ran down the housing’s length and were each fixed with an external nut, which would often seize after a short time in seawater – opening these instruments often required a hacksaw. This design soon gave way to a version that resembles the first SBE 19, which repositioned the conductivity cell to the side and abandoned the aluminum rods.
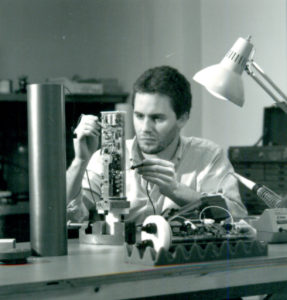
Dave Walter: “That photo was taken and used for an article about an upstart instrument company called Sea-Bird. I think I was about 26 years old at the time and two weeks into growing my first beard. At the time we had a total of 10 people working at the Bird and that included the owners. The instrument I am poking probes at is one of the first SBE-19s ever built.”
Around 2000, Senior Mechanical Engineer Dave Walter (shown above) was tasked with designing the next generation of the SeaCAT family. Sea-Bird’s team made some electronic improvements and abandoned the aluminum housings, offering the 16plus and 19plus in acetyl plastic and titanium, having gained more experience with titanium while developing MicroCAT CTDs. Most noteworthy, the new design included a plenum connecting the temperature probe to the conductivity cell that significantly reduced salinity spiking.
Today, Dave’s redesign is mechanically identical to the modern SeaCATs, the 16plus V2 and 19plus V2.
The Seakittens
A short lived spinoff from the SeaCATs, the “SeaKittens,” were designed to be neutrally buoyant without a battery pack for deployment from sea ice. Sea-Bird did not manufacture many of these. This design predated modern finite element analysis, so Dave had no way to estimate whether these were going to be neutrally buoyant. According to him:
“I had no way to estimate whether this thing was going to be buoyant or not. I removed as much of the material from the design as I possibly could, and I just built one. We threw it in the tank and I hit the bullseye. It was spot on.”
Related Posts
Featured Posts
Oceanology International 2024
We hope to see you at #Oi24 We are excited to return to Oceanology International 2024 again in London, UK from March 12-14. Overview Oceanology International brings together 500+ exhibitors in the only event that links the three key players in the industry:...
Ocean Sciences Meeting 2024
We hope to see you at #OSM24 We are excited to return to Ocean Sciences Meeting 2024 in New Orleans, Louisiana from February 18-23 at booth number #527. Overview The Ocean Sciences Meeting 2024 is co-sponsored by the American Geophysical Union, the Association for the...
Pride 2023
Celebrating and honoring our LGBTQIA+ communities At Sea-Bird Scientific, we are proud to stand with members of the LGBTQIA+ community during Pride Month 2023. As with last year, we changed our logo on social media to feature a rainbow throughout the month of June in...
Science and Technology
Platform